How to choose heat shrinkable film during packaging of heat shrink packaging machine
How to Choose Heat Shrinkable Film for a Heat Shrink Packaging Machine
Heat shrink packaging, also known as shrink wrapping, is a popular method used in the packaging industry. It involves using a heat shrinkable plastic film that is wrapped around a product or placed over the opening of a container. As the packaged item passes through a heating chamber or a heat tunnel, the film shrinks due to the heat, tightly conforming to the shape of the product. This process not only enhances the visual appeal but also provides protection and tamper resistance.
Selecting the right heat shrinkable film is crucial for the effective operation of a heat shrink packaging machine. The film must have a balanced shrinkage rate in both the longitudinal and transverse directions. The shrinkage rate is calculated as (L1 - L2) / L1 × 100%, where L1 is the original length, and L2 is the length after being immersed in water at 120°C for 1–2 seconds. Most heat shrinkable films are manufactured by stretching the material during production and then cooling it. When reheated, they return to their original size, which makes them ideal for packaging. A typical shrinkage rate of around 50% in both directions is recommended, along with good heat seal strength, tensile strength, impact resistance, tear resistance, and adequate moisture and oil resistance.
Common materials used for heat shrinkable films include polyvinyl chloride (PVC), polyethylene (PE), polypropylene (PP), polyvinylidene chloride (PVDC), polyester (PET), polystyrene (EPS), and ethylene-vinyl acetate copolymer (EVA). Each material has its own characteristics and applications, depending on the product being packaged. For example, PVC is widely used for its flexibility and clarity, while PET offers excellent durability and transparency.
Compared to regular plastic films, heat shrinkable films offer better strength, transparency, and elongation. When heated, these films can stretch up to 4:1 or 7:1 before shrinking, whereas regular films typically stretch only 2:1. There are two main types of heat shrinkable films: biaxially oriented films, which shrink evenly in both directions, and uniaxially oriented films, which shrink in one direction only. Biaxial films are often used for fresh food, tray packaging, and container sealing, while uniaxial films are suitable for labeling bottles, sealing containers, and packaging products like fruits and vegetables.
The advantages of heat shrink packaging include fast processing, high efficiency, low cost, ease of use, and convenient transportation and sales. Due to these benefits, it is widely used in the food industry, especially for products that require an attractive and protective outer layer.
For more information, visit Swift Shrinking Machine: http://
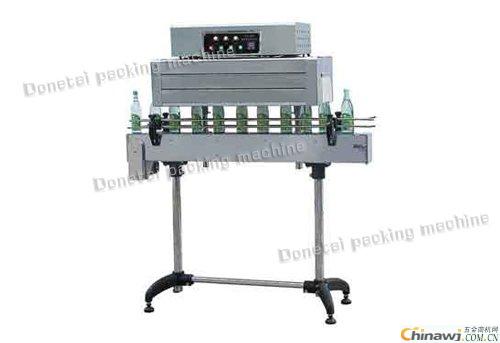
UV accelerated aging test chamber
A UV accelerated aging test chamber is a specialized piece of equipment used to simulate the effects of long-term exposure to ultraviolet (UV) radiation on various materials and products. It is commonly used in industries such as automotive, aerospace, cosmetics, and electronics to evaluate the durability and performance of materials under accelerated aging conditions.
The chamber typically consists of a controlled environment with UV lamps that emit high-intensity UV radiation, simulating the UV exposure that materials would experience over an extended period. The UV lamps produce a spectrum of UV light, including UVA, UVB, and UVC, which can be adjusted to mimic specific environmental conditions.
The test specimens or products are placed inside the chamber, and the UV lamps are turned on to initiate the aging process. The chamber may also incorporate other environmental factors such as temperature, humidity, and airflow to simulate real-world conditions more accurately.
The accelerated aging process allows manufacturers to assess the effects of UV radiation on the materials' physical, chemical, and mechanical properties. It helps determine the degradation, discoloration, embrittlement, cracking, or other changes that may occur over time due to UV exposure.
UV accelerated aging test chambers are essential for quality control, product development, and compliance with industry standards and regulations. They enable manufacturers to evaluate the performance and lifespan of materials, optimize formulations, and make informed decisions about product design, materials selection, and UV protection measures.
UV aging test chamber, UV accelerated aging test chamber, UV test chamber
Dongguan Best Instrument Technology Co., Ltd , https://www.best-tester.com