Renishaw probe significantly reduces Equinox 3D manual intervention time
As a professional manufacturer of fiberglass products for customers in different industries, Equinox 3D often receives production orders for various complex and customized products from customers. Thanks to the introduction of the Renishaw probe measuring system in the manufacturing process, the company in Farfsham, UK has the ability to accurately and reliably meet the unique needs of its customers within the strict delivery deadlines.
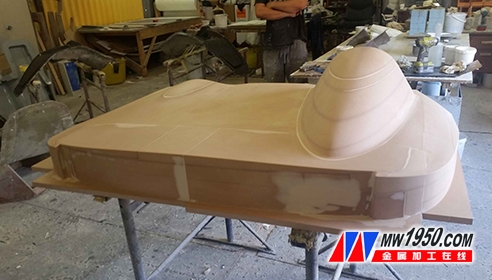
The 16 model plates must be assembled accurately to ensure that the final fiberglass top shape meets the requirements and requires minimal manual dressing and sanding.
background
Equinox Products started out as a manufacturer of fiberglass products for a variety of industries, including automotive, construction and even playground equipment. Due to the stable demand for molds in the production process, the company founded a subsidiary, Equinox 3D. The new company continues to grow and now offers four-axis CNC machining, 3D scanning, reverse engineering, CAD design and other engineering services unrelated to mold making.
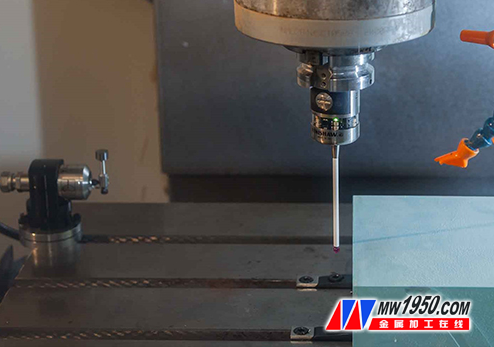
Equinox 3D uses the Renishaw OMP40 workpiece alignment probe to set the respective reference points for 16 polyurethane (PU) model plates with a density of 0.7
Equinox 3D's newly added XYZ 1020 Vertical Machining Center (VMC) is equipped with a Renishaw OMP40 workpiece alignment probe and a TS27R tool setting tool, which greatly enhances the company's productivity. Although Equinox 3D is capable of accepting tolerances of ±0.1 mm (rather than strictly to the micron level), they still believe that the probe measurement system is a useful complement to its manufacturing process. Because consumers directly see and touch the glass fiber products they produce, the aesthetic appearance is critical. Most of the Equinox 3D products are segmented and then assembled, which means precise alignment is critical. In the past, the polishing, assembly and finishing of a multi-segment product took several hours to complete, even without a few days of labor. This will add a lot of time and cost to the production process, and time is a luxury for Equinox 3D. A recent urgent work of delivery time is a typical example.
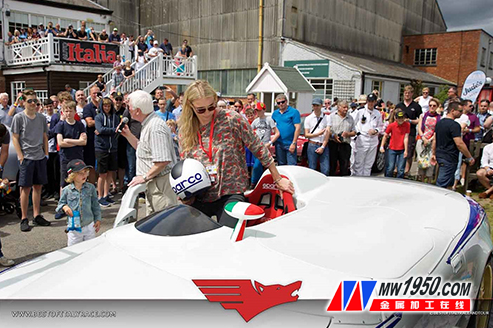
Supermodel and racing driver Jodie Kidd unveiled the mystery of this super single-seater in Brooklands
challenge
“The organizer of the 'Most of Italy' carnival event suddenly found us – this is a two-day racing carnival at Emilia-Romagna Piacenza in Castell'Arquato, the climax is a super variety from Italy "Climbing competitions for sports cars, superbikes and bicycles," said Darren George, technical director of Equinox 3D. "The organizer asked us to convert a Maserati sports car into a concept car - Super Monoposto.
The prototype of the concept car was the production version of the Maserati 4200, but the organizer used an angle grinder to remove the soft roof and windshield. “The date of the carnival is already well established; in addition, some fixed workflows take some time, so the time left for us is only a few weeks, we have to be the single-seat sports car during this period. The cockpit is designed and manufactured with a new fiberglass roof that prepares the car for appearance at the Brooklands, where it will be driven by supermodel and TV presenter Jodie Kidd to complete the debut," Darren George explained.
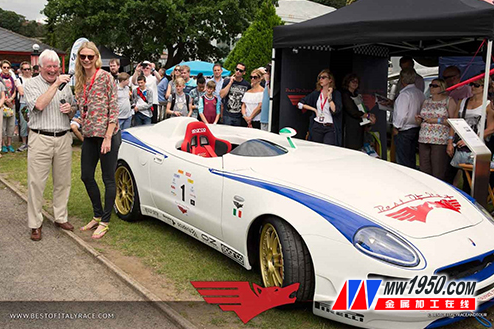
Renishaw probe significantly reduces Equinox 3D manual intervention time
The newly designed top cover extends from the rear of the sports car and covers the passenger seat, leaving only the driver's seat exposed. Equinox 3D needed to produce a multi-section fiberglass top cover; this top cover consisted of a total of 16 model panels. All model panels must be accurately assembled to ensure that the final fiberglass top cover conforms to the requirements and requires minimal manual sanding.
“We can easily and accurately know whether the actual machining dimensions are consistent with the CAD data, and the probe measurement data can be seamlessly interfaced with the CAD data, which is an invaluable advantage for us. This fiberglass top cover must be installed in a seamless manner. In the sports car, the probe measurement system gives us the confidence to complete the work smoothly." - Equinox 3D (UK)
solution
The Equinox 3D uses the Renishaw OMP40 workpiece alignment probe to set the respective reference points for the 16 polyurethane (PU) model plates with a density of 0.7. With the probe measurement system, setting a reference point for each model board takes approximately one minute. In the past, even if you simply set the reference points for the X and Y axes, the set time for each axis takes 3-4 minutes, and it takes even up to five minutes to set the Z axis reference point.
In the processing of this fiberglass top cover consisting of 16 model plates, an OMP40 workpiece alignment probe and a TS27R tool setter are used to complete the setting process.
The Renishaw probe saved approximately three hours for the Equinox 3D in terms of set-up time. Considering the urgency of this working time, the measurement system is very helpful for Equinox 3D. “We have to start the machine 24 hours a day for 10 days in a row to make the top cover as planned, which means we have to go to the workshop at midnight to set up the next model board. The Renishaw probe can automatically set the reference point. This has helped us a lot," Darren George said.
Since most of its products are irregular in shape, Equinox 3D also makes full use of the Renishaw OMP40 probe for in-machine post-sequence detection and uses the probe to confirm that the reference point matches the CAD data before removing the workpiece from the machine. . Similarly, Equinox 3D uses the Renishaw TS27R tool setting tool to confirm and modify the mid-range tool compensation. This is an insurance for the accurate machining of qualified parts at one time.
result
Although the Equinox 3D saves a lot of in-machine machining time by using the Renishaw OMP40 probe, the time saved for assembling the 16 model panels into a complete top cover is even more impressive. Darren George has estimated that for this type and size of fiberglass products, manual dressing and sanding time typically takes one to two days. Thanks to the high precision of the initial processing, the actual situation is that they hardly need to be manually trimmed. This means that the assembly work is very simple, because each adjacent part fits tightly.
“Time is the biggest challenge for this job, and we ended up delivering the finished and painted sports car roof 12 hours in advance. Without a probe measurement system, this is simply not possible. In this project Due to the time, we only have one chance to make this top cover. The finished product is 2.4 meters long and contains many irregular 3D shapes. We don't have any ready-made CAD data, all of which will cause people to worry about tolerance." Mr. George explained, “Although we do not have to strictly limit the tolerance to the micron level, we still need to ensure that the fiberglass top cover fits perfectly into the sports car. The probe measurement system gives us confidence to get the job done. ."
Although the company also uses 3D non-contact scanning technology to measure workpieces, scanning technology still has some limitations for some small internal features. At this time, Equinox 3D will once again use the Renishaw OMP40 probe to precisely set the reference points for these features. This feature is especially useful when reverse engineering complex workpieces. The company's most recent project involved the production of bell-shaped housings for the assembly of gearboxes. Without the relevant functions provided by the Renishaw probe measurement system, the manufacturing process would be very difficult.
About Renishaw
Renishaw is one of the world's leading engineering and technology companies with expertise in precision measurement and healthcare. The company supplies products and services to a wide range of industries and sectors – from aircraft engines and wind turbine generators to dental and brain surgery medical devices. In addition, it is a leader in global additive manufacturing (also known as 3D printing) and is the only company in the UK to design and manufacture industrial additive manufacturing equipment ("printing" parts with metal powder).
The Renishaw Group currently has more than 70 branches in 35 countries and employs more than 4,000 people, of whom more than 2,700 work in the UK. Most of the company's R&D and manufacturing is carried out in the UK. In the 2016 fiscal year ending June 2016, Renishaw achieved sales of £436.6 million, 95% of which came from export business. The company's largest markets are China, the United States, Germany and Japan.
Medical Items Protective Clothing
Anti Coronavirus Medical Items Protective clothing medical Items
Fabric :It is made of non-woven fabric ,with cutting and sewing.Non-sterile,disposable use.
Intended use:It is used for general isolation in the clinics,wards,examination rooms,and public places of medical institutions.
Protective suit,Protective clothing medical,Medical isolation suit,Medical protective clothing
Hebei TongChan Imp.&Exp.Co., Ltd. , https://www.tongchanmesh.com